What Do You Pour In Ceramic Molds?
Ceramic molds are used in a variety of casting processes to create metal parts and tools with high dimensional accuracy and fine details. Ceramic mold casting involves pouring molten metal into a ceramic mold to produce an accurate casting.
The purpose of this article is to provide an overview of the different types of materials that can be poured into ceramic molds for casting. We will explain the various ceramic mold casting processes used with metals, waxes, resins, plasters, and even foods. Understanding the capabilities of ceramic molds for precision casting can help designers and engineers select the optimal process for their application.
Slip Casting
Slip casting is a popular method of making ceramics pieces using liquid clay, known as slip. The slip casting process involves pouring liquid clay slip into porous plaster molds. As the slip is absorbed into the mold walls, it leaves a layer of solid clay against the mold surface that forms the final piece.
There are two main types of liquid clay slips used in slip casting:
- Pottery slip – This is a suspension of clay particles in water, usually around 15-20% clay by weight. Pottery slips produce items like tableware, tiles, and decorative pieces.
- Porcelain slip – Made from kaolin clay, feldspar, and quartz. Porcelain slips are used to make items like sanitaryware and electrical insulators that require high strength and low porosity.
The plaster mold rapidly absorbs water from the slip leaving a layer of solid clay in the shape of the mold’s interior. Once the desired thickness is achieved, the excess slip is poured out of the mold. The cast piece is then removed from the mold and allowed to dry before firing in a kiln.
Slip casting allows intricate, detailed shapes to be molded consistently and efficiently (Source). The process is ideal for making complex forms or multiple reproductions of the same item.
Press Molding
Press molding is a popular casting technique for reproducing ceramic pieces in large quantities. In press molding, liquid clay slip is poured into a plaster mold and allowed to absorb water, forming a layer of clay on the mold surface. Once the desired thickness is achieved, the excess slip is poured out of the mold. The mold is then placed in a mechanical or hydraulic press, which applies pressure and compresses the clay. This compacts the clay and pushes out any remaining water. The clay will retain the exact shape of the mold.
The liquid clay used for press molding is called slip. Slip is composed of clay, water, and additives that help regulate viscosity and workability. Common recipe components include clay, ball clay, kaolin, bentonite, and sodium silicate. The specific ratios vary based on the clay body and desired properties. A typical press molding slip contains around 20-40% clay solids in water.
Some key qualities to consider for press mold slip are viscosity, plasticity, absorption rate, drying time, and fired strength. The slip needs to flow well enough to completely coat the mold surface, but also hold its shape once pressed. Fast water absorption allows the clay layer to quickly set up in the mold. Slow drying prevents cracks. High fired strength produces a durable final ceramic piece.
Resin Casting
Resin casting is a popular method for creating detailed casts in ceramic molds. The liquid resin is poured into the mold and then hardens to create an accurate cast replica. There are several types of resin that can be used:
- Polyester resin – This is an inexpensive resin that can be colored. It cures quickly but can shrink slightly during curing which may reduce detail quality. Polyester resin can be purchased at most craft stores. (https://en.wikipedia.org/wiki/Resin_casting)
- Epoxy resin – Epoxy creates extremely accurate casts with excellent detail reproduction. It’s more expensive than polyester but is the preferred choice for high quality resin casting. Epoxy has a longer cure time but less shrinkage. (https://tethon3d.com/product/castalite-ceramic-shell-resin/)
- UV-cured resin – This specialized resin cures under ultraviolet light, allowing rapid casting. It’s most commonly used in high volume commercial applications. UV resin offers very high accuracy. (https://www.youtube.com/watch?v=CWF_ornyLjY)
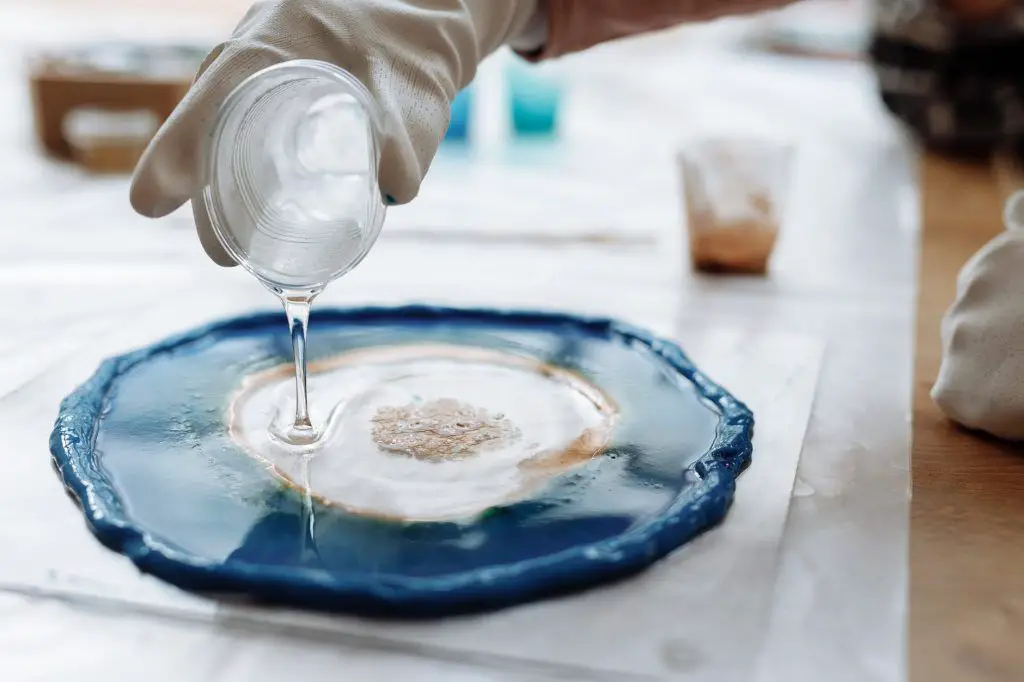
When selecting a resin, factors like cost, cure time, shrinkage, and clarity should be considered. The mold material and intended use of the cast should also influence the choice. With multiple resin options available, ceramic mold casting offers the flexibility to achieve extremely detailed resin casts for art, jewelry, prototyping, and other applications.
Metal Casting
Metals commonly used with ceramic mold casting include aluminum, copper, bronze, brass, iron, and steel 1. The metal is melted and poured into the ceramic mold. When the metal solidifies, it takes on the precise shape of the mold’s cavity.
Ceramic molds can withstand very high temperatures, allowing them to be used with almost any metal. The heat resistance, along with the molds’ strength and porosity, make ceramics ideal for producing detailed and accurate metal castings.
Some key metals used in ceramic mold casting include:
- Aluminum: Lightweight yet strong, aluminum is one of the most widely cast metals. It has excellent corrosion resistance and ductility.
- Steel: With high strength and hardness, steel is commonly cast into parts like gears, valves, and engine components. Stainless steel offers additional corrosion resistance.
- Bronze: An alloy of copper and tin, bronze offers strength, corrosion resistance, and attractive colors. It’s used for artistic castings and bearings.
- Brass: Brass is an alloy of copper and zinc valued for its strength, machinability, and corrosion resistance. It has decorative and engineering applications.
The natural porosity of ceramic allows gas and air to escape from the molten metal, resulting in smooth, pore-free castings. Ceramic molds can produce castings with excellent detail and dimensional accuracy.
Wax Casting
Lost wax casting, also called investment casting, is a process that has been used for thousands of years to create detailed metal parts. It gets its name from the use of wax to create a pattern which is then surrounded, or invested, into a ceramic shell mold. The wax is melted out, or lost, to leave a cavity into which metal can be poured.
The lost wax casting process involves the following steps:
- A wax model is created by injecting wax into a rubber mold or hand sculpting.
- Sprues and risers are attached to the wax pattern to allow the molten metal to flow through and compensate for shrinkage.
- The wax model is immersed repeatedly in ceramic slurry to build up a multi-layer shell around it.
- The wax is melted out in a furnace, leaving a hollow mold.
- Molten metal is poured into the mold to fill the cavity.
- Once cooled and solidified, the ceramic shell is broken away.
- The casting is cut off from the sprues and cleaned up.
Lost wax casting allows for excellent recreation of fine details from the wax model in the final metal casting. It is commonly used for jewelry, dental crowns, sculptures, and mechanical parts. The process requires specialized equipment and skills but can produce intricate, high-quality metal castings.[1]
Plaster Casting
Plaster casting is a common technique for creating ceramic molds. The main ingredients in plaster used for casting are calcium sulfate hemihydrate, commonly known as plaster of Paris, and water. When these ingredients are mixed, a chemical reaction occurs causing the plaster to set into a solid. The setting time can be controlled by varying the plaster to water ratio.
The plaster casting process involves several steps:
- First, create a positive model out of clay or another material. This is the object you want to cast.
- Build a containment box around the model and coat the model in a mold release agent so it can be removed later.
- Mix the plaster according to the manufacturer’s directions and pour it into the containment box, fully covering the model.
- Allow the plaster to fully set, which can take 20 minutes or more.
- Carefully separate and remove the model from the hardened plaster mold.
- The mold is now ready to have liquid casting slip poured into it.
- Once the slip has hardened, open the mold and remove the cast ceramic piece.
Plaster can be reused for multiple castings if properly cared for. It provides an affordable and accessible means of reproducing ceramic models.(1)
Concrete Casting
Concrete can be used to cast ceramic molds as it is an inexpensive and versatile material (https://www.youtube.com/watch?v=7IlChMOG738). When casting concrete in a ceramic mold, it is important to choose the right concrete mix. Pre-mixed concrete is the easiest option as it already contains the proper ratios of cement, sand, and aggregate. For more control, some people prefer to mix their own concrete using Portland cement, sand, gravel, and water (https://www.etsy.com/market/concrete_casting). The concrete mixture should be thick enough to hold its shape when poured into the mold. When working with concrete, proper safety precautions should be taken such as wearing a respirator mask and gloves.
When casting concrete, spray the ceramic mold with a release agent or coat with petroleum jelly to prevent the concrete from sticking. Slowly pour the concrete into the mold, tapping the sides gently to remove air bubbles. Allow the concrete to cure fully, which can take 1-2 days, before removing it from the mold. Concrete shrinks slightly when drying so a mold can only be used a few times before it wears out. With the right cement mixture and mold preparation, concrete can create durable cast ceramic pieces.
Food Casting
Food casting refers to making edible molds to shape foods like chocolate, sugars, or ice. Common edible ingredients used in food molds include gelatin, chocolate, gum paste, isomalt, sugar, and ice. Gelatin is a popular choice as it melts at body temperature, allowing the shaped food to easily release from the mold. Chocolate and gum paste also make sturdy, detailed molds. Isomalt, a sugar substitute, can be boiled and poured into molds for sugar shaping. Pure ice can even be carved into shapes to mold foods. When choosing ingredients, it’s important to pick edible materials that will hold their shape at room temperature or in the fridge/freezer. The mold material must also be food safe and not contain any toxic chemicals. Proper food handling and sanitization is critical when casting edible molds to prevent contamination.
Conclusion
When deciding what to pour into ceramic molds, there are several options to consider. For clay slip casting, liquid clay slips are used to form the desired shape inside plaster molds. Press molds use clays in a more solid form that are pressed into molds. Resin casting involves pouring liquid resin into molds to create detailed castings.
For metal castings, molten metals like bronze or aluminum are poured into ceramic molds. Wax casting uses hot molten wax to form shapes. Plaster casting utilizes liquid plaster poured into molds to create plaster castings. Concrete casting employs liquid concrete poured into molds to form concrete products. Even food ingredients like chocolate or gelatin can be poured into molds to create edible castings.
Each material has its own advantages and disadvantages. Liquid clays, resins, and metals allow for highly detailed castings but require more specialized equipment and safety measures. Wax, plaster, and concrete are simpler to use but may lack fine details. Food castings are edible but not durable. Overall, the liquid material chosen depends on the desired characteristics of the final ceramic casting.